ZF demonstrates the potential that resides in particular in the combination of electromobility and lightweight design strategies by unveiling its innovation prototype based on a subcompact car. With the concept presented in early June 2013, lightweight suspension components supplement the electric axle drive including inverter, thus increasing both the range and the driving dynamics of the electric vehicle.
The electric drive in the ZF innovation prototype is tailored to future requirements of urban traffic. The drive module, which is located centrally on the axle, has 90 kW mechanical power and develops high torque even at low speeds. The electric axle module can be used as an efficient drive for purely electric subcompact and compact cars or as an electric rear axle in the axle hybrid.
For the innovation prototype, ZF has tailored lightweight construction in the chassis optimally to the specific requirements of electromobility: Weight saving directly helps increase the range or payload of electrically driven passenger cars. Cutting weight and reducing unsprung masses however also offers advantages for conventionally powered vehicles since this setup reduces fuel consumption while increasing driving dynamics.
On the front axle of the ZF innovation prototype a suspension strut and knuckle module made from fiber-reinforced plastics (FRP) provides damping and wheel guidance. Innovative FRP design ensures a smooth surface. The weight saving of up to 40 percent compared to the standard steel version is enormous.
A self-aligning support with hybrid design also replaces the conventional steel component for the front axle of the innovation prototype. ZF helps save up to 16 percent weight here through the combined usage of carbon fiber (CRP), injection-molded polyamide, and high-strength steel.
With an innovative semi-independent rear suspension, the ZF engineers not only reduce weight in the innovation prototype; they also increase the variability. Thanks to a flexible stabilizer concept, the roll behavior can be tailored specifically to customer requirements. This interface enables FRP stabilizers to be mounted, thus saving additional weight – up to 50 percent for instance in the case of the CRP stabilizer. The ZF semi-independent rear suspension is made out of steel and carbon fiber reinforced plastic. It is ideally combined with ZF lightweight dampers. These are 25 percent lighter than conventional dampers, thanks to the usage of aluminum in combination with plastic-coated damper mounts and an optimized design.
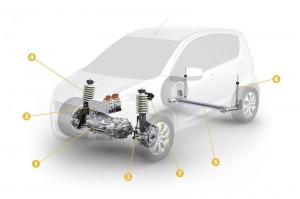
Source; ZF