With much talk about economical vehicles, often the processes used to manufacture and build them are forgotten. Not so at Nissan who have set out a global environmental initiative, the Nissan Green Program 2016.
In an incredibly wordy sentence, the program, ‘focuses on reducing environmental impacts of corporate activities and pursuing harmony between resource consumption and ecology by promoting and widening the application of innovative green technologies, energy management and fuel-efficient vehicles.‘
Rather than try to explain that, it’s easier to show how Nissan are going to do what they’ve set out to achieve.
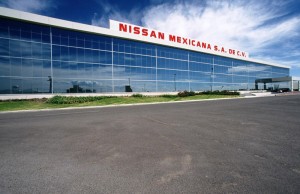
In Mexico, Nissan’s Aguascalientes Vehicle Assembly Plant already uses 50% of it’s energy requirement from renewable resources including wind and landfill gas power. Not only does the use of these renewable energies reduce pollutants from the factory, but they have also saved Nissan 10% in utility costs.
Nissan is, as are all, a manufacturer of automobiles set up to make a profit. So, although their green credentials are already good, Nissan are not just stopping there. Instead, Nissan are actively looking to make more use of renewable energy – and who can blame them if a bit of wind and waste created gas can save a whopping 10% in utility costs at just one factory, imagine that same 10% applied to reductions in costs at all of their factories around the world. As a result, the Mexico plant is looking at other renewable sources to balance and compensate for times when there is not much wind power provided, or the city has run out of waste.
The green energy program will be extended to the Cuernavaca Vehicle Assembly Plant and to the new Aguascalientes 2 assembly plant scheduled to open later this year.
Meanwhile, in the United States Nissan is a leader in energy performance with three new U.S. Environmental Protection Agency (EPA) ENERGY STAR® accolades on the shelf, including the 2013 Partner of the Year – Sustained Excellence Award, the highest honor given to select organizations that are dedicated to protecting the environment through energy efficiency. Bill Krueger, Nissan’s senior vice president of Manufacturing, Purchasing, Production Engineering and Supply Chain Management, said,
“Since becoming an ENERGY STAR partner in 2006, we have saved more than 800 billion BTUs (British thermal units) in our vehicle assembly process, that’s enough energy to power the all-electric Nissan LEAF for more than 750 million miles.”
This award closely follows two other ENERGY STAR achievements for Nissan’s powertrain plant and vehicle assembly facilities.
Nissan’s powertrain plant in Decherd, Tennessee, recently achieved the EPA’s ENERGY STAR Challenge for Industry recognition for reducing the amount of energy needed to assemble engines by 7 percent in just 12 months by investing in more efficient equipment and establishing a compressed air leak reduction program – compressed air is used by a large proportion of the machinery and tools in manufacture, which is itself created by a compressor requiring large amounts of energy to compress the air in the first place.
This kind of innovative thinking has seen Nissan’s vehicle assembly plants in Smyrna, Tennessee, and Canton, Mississippi, awarded the ENERGY STAR Certification for the seventh year in a row, signifying Nissan’s spot among the top 25 percent of the automotive manufacturing industry for superior energy management.
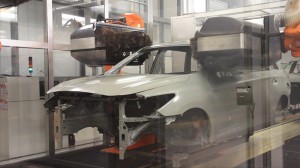
With the recent additions of Infiniti QX60 and Nissan LEAF, and with production of Nissan Rogue on the way to the Nissan vehicle assembly plant in Smyrna, Tennessee, the company has added its most advanced paint plant in the world that sets new standards for quality, efficiency and environmental impact. In fact, the new paint plant is capable of reducing energy consumption by 30 percent, carbon emissions by 30 percent and volatile organic compound (VOCs) emissions by 70 percent.
In Brazil on the other hand, there is the soon to open new Resende manufacturing plant. In the first half of 2014 it will open as one of the most sustainable facilities in the world. The plant features a ‘Green Belt’ that circles the entire facility and is designed to help neutralize C02 emissions while also reducing noise levels of the factory for the surrounding environment. Construction of wetlands also will help to balance the area ecosystem.
The future
Nissan Green Program 2016 promotes activities not only in development and manufacturing departments associated with the production of automobiles, but also in sales, service and all other departments of the company. Even with its plans to increase sales volume globally, Nissan forecasts that through the initiative CO2 emissions from its new vehicles and corporate activities will peak in the 2020s and then subside while the volume of new natural resources used will be maintained at the level of the 2010s.
Source; Nissan